april, 2024
Boldly Moving Makers Forward.
Inaugural Sustainable Aviation Fuel Conference Highlights Opportunity for Renewable Fuel to Lower Emissions and Transform Industries
FOR IMMEDIATE RELEASE March 21, 2024 Inaugural Sustainable Aviation Fuel Conference Highlights Opportunity for Renewable Fuel to Lower Emissions and Transform Industries Inaugural conference will discuss latest in scientific research,…
Read More
Key Partners
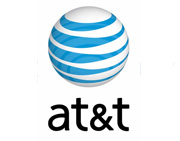
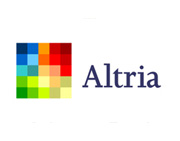
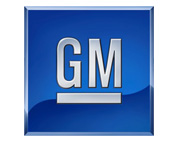
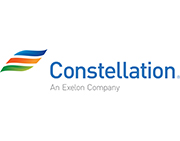
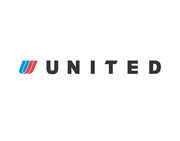
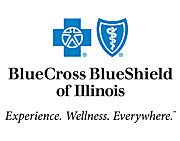
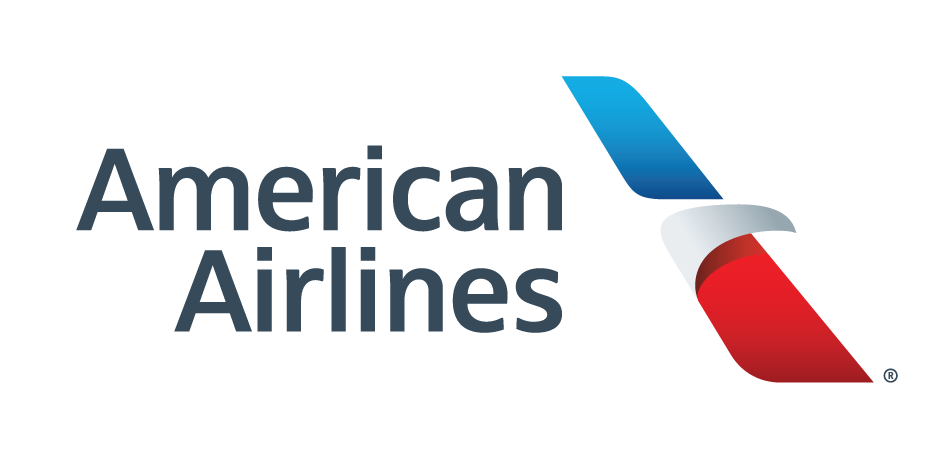
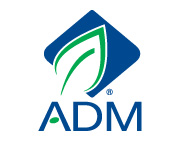
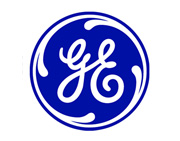
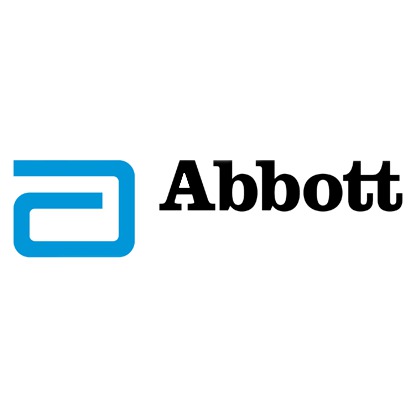
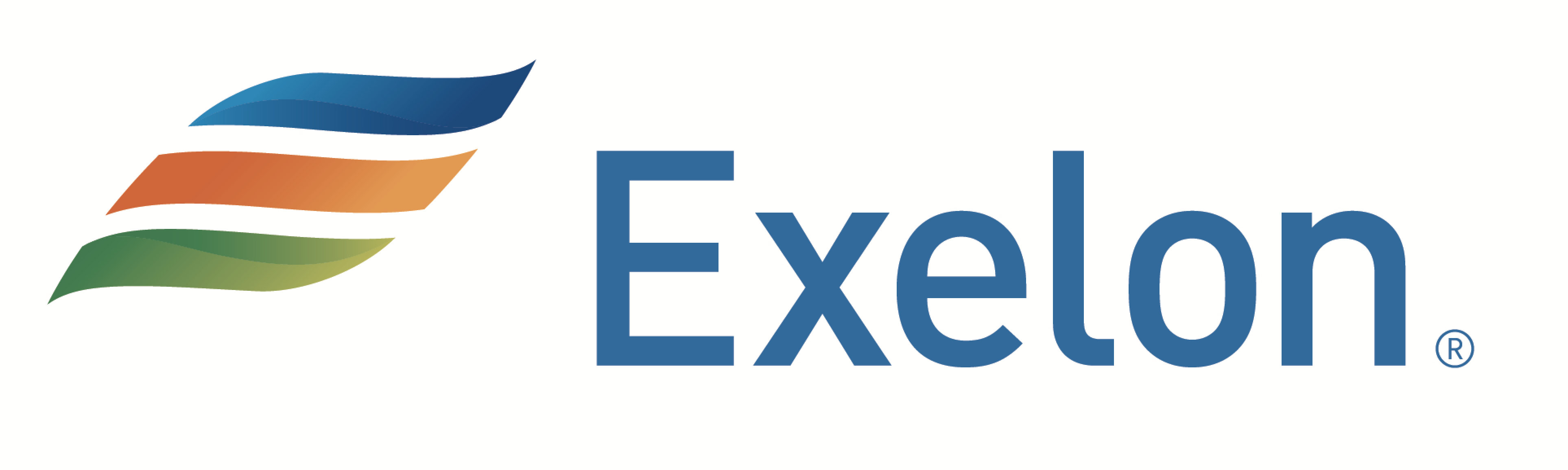
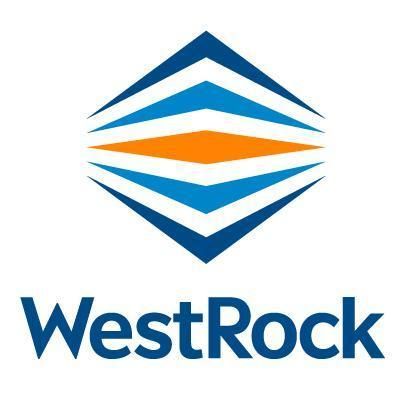

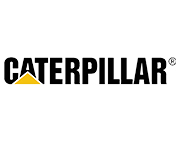
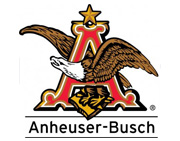
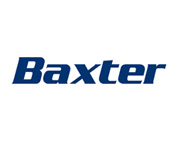
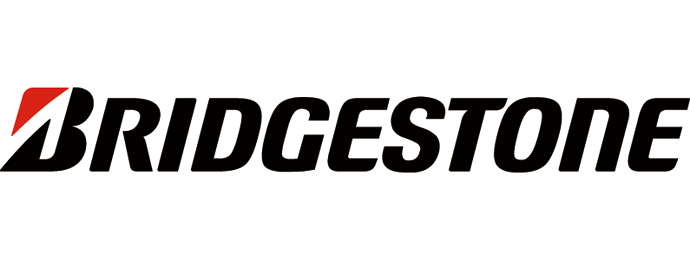
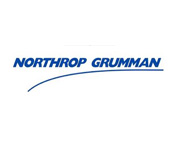
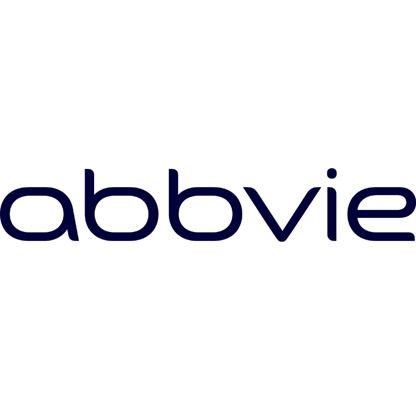
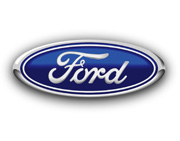
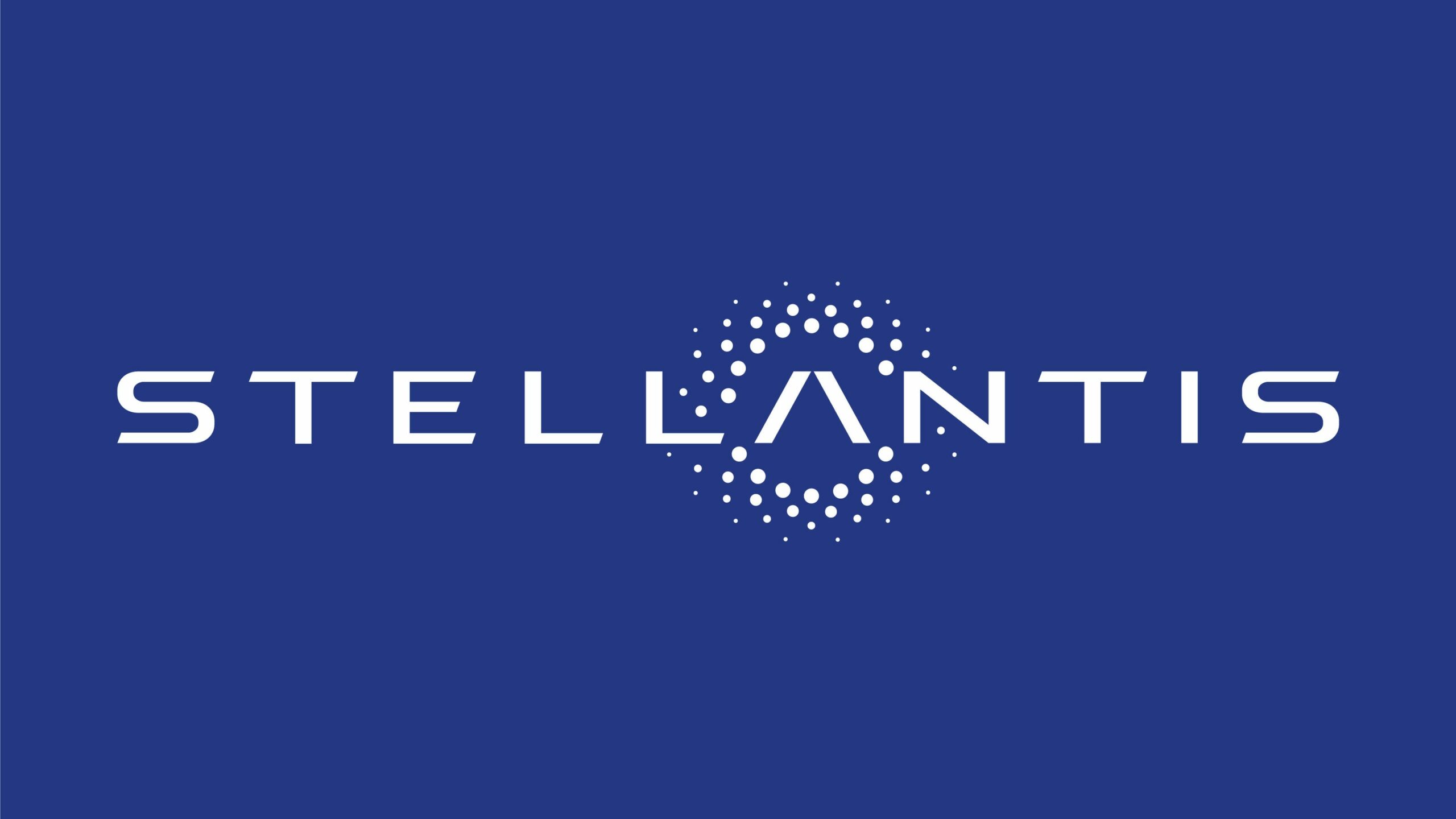
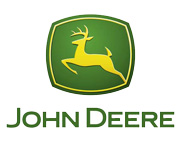
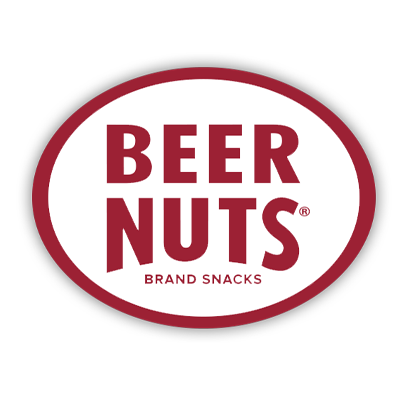
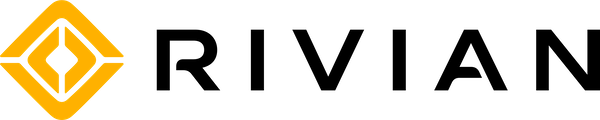
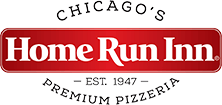

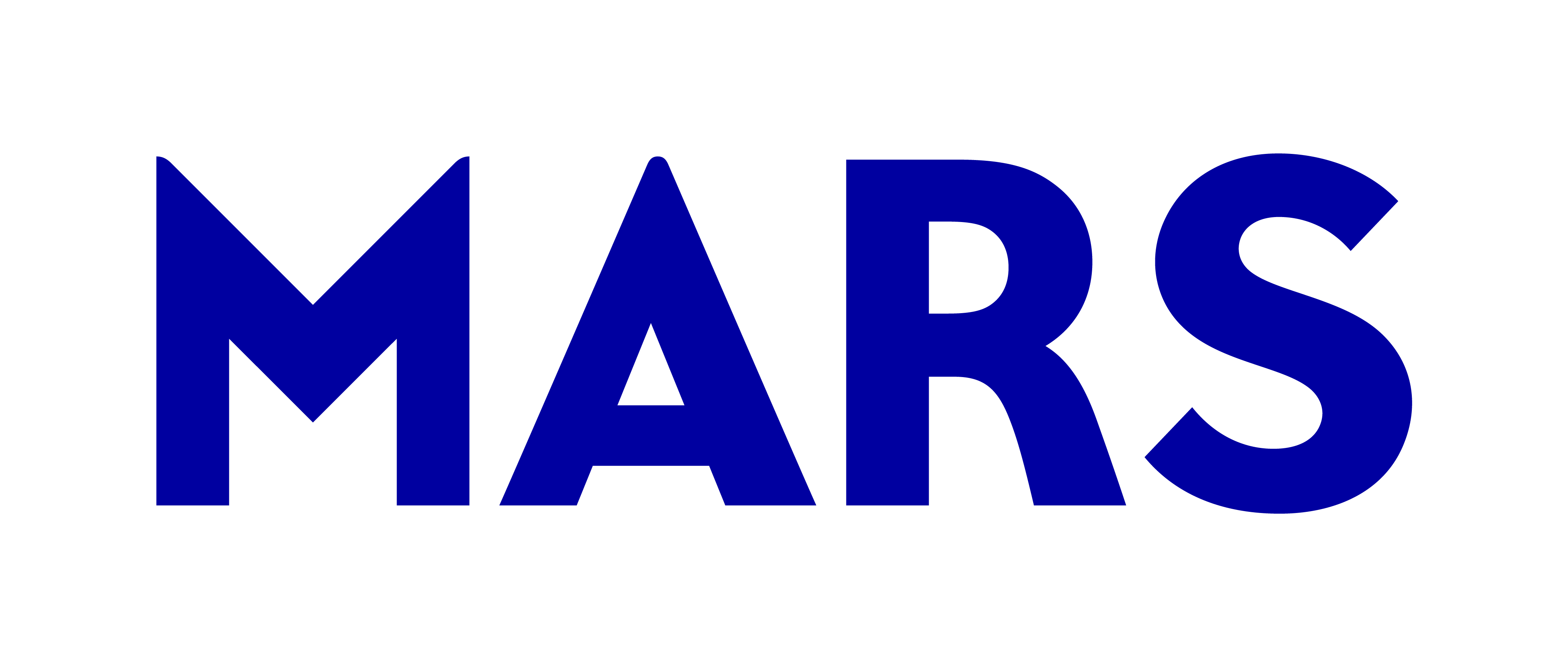
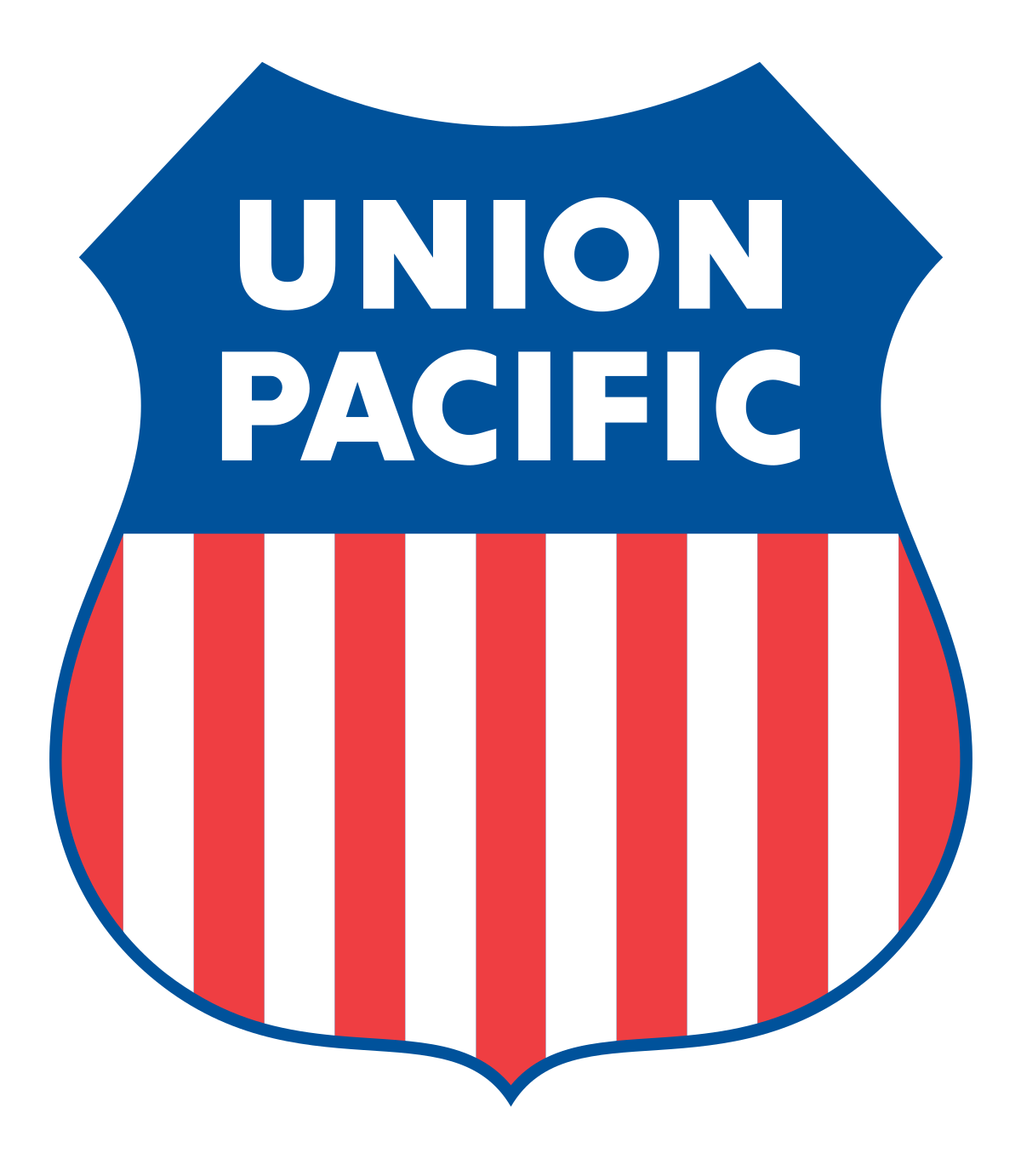
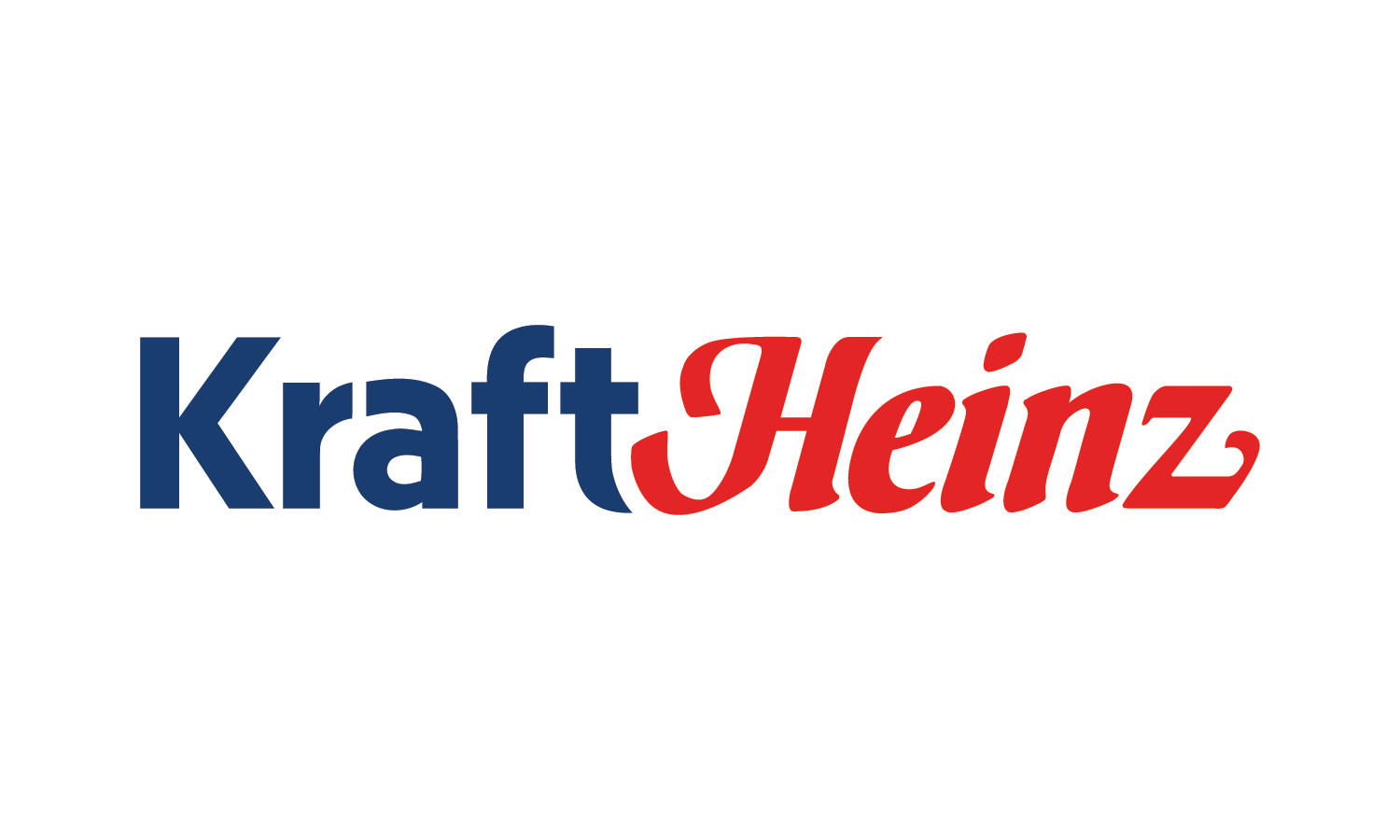
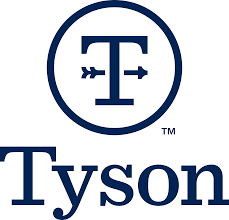
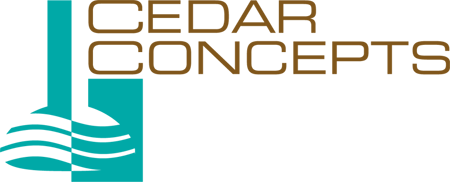
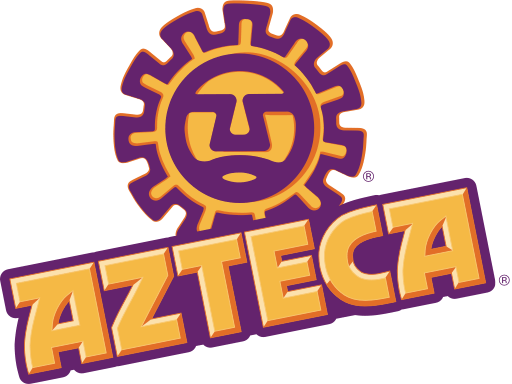
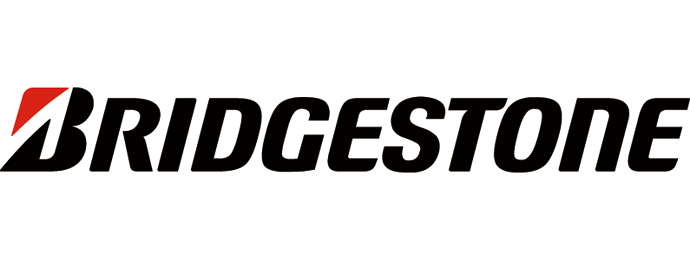